Characterizing CMP Polish Rates with
MetaPULSE-II
Introduction
As the semiconductor industry transitions from aluminum to copper
interconnects, the Chemical Mechanical Planarization (CMP) process
is being redefined. In traditional aluminum processing, excess SiO2
interlevel dielectric (ILD) overcoats the preformed (plasma etched)
aluminum interconnect ˇ§wiresˇ¨, so CMP does not reduce aluminum line
thickness. In the copper dual-damascene process, CMP removes excess
electrochemically deposited (ECD) copper, forming the interconnect
wires and interlevel vias. CMP provides the planarity necessary for
the subsequent level of via/interconnect structures, but, if not
adequately controlled, may thin the copper lines. The copper
dual-damascene process requires CMP to polish three different
materials, the ECD copper, the Ta, TaN, or other barrier material,
and the ILD (or low-k ILD). Because each of these materials has
different hardness and chemistry, they have different polishing
rates. Developing the appropriate pads and slurry mixes to correctly
process all three materials and maintaining the desired polishing
rates during high volume manufacturing is a significant challenge.
Metrology tools that can precisely characterize and monitor the
copper CMP process on product wafers at semiconductor production
throughput rates will be an important requirement for manufacturers
making copper interconnect devices.
Background
Because copper can not be etched directly, the dual-damascene
process is being used for copper interconnect manufacturing. In
dual-damascene, both vias and trenches are etched into the ILD. A
thin barrier layer and a copper seed layer are then deposited over
the etched ILD. Next, ECD copper is used to fill the vias and
trenches until a thick copper blanket covers the entire surface of
the wafer. CMP then polishes the wafer, ideally stopping just after
the barrier layer is cleared in all areas (and over all types of
structures) across the wafer, isolating the copper wires in their
ILD trenches. Determining the exact end point for the CMP process
can be difficult. A main reason for this is different structures
polish at different rates. Figure 1 shows several of the common
problems encountered in copper dual damascene CMP processing.
Dishing occurs when large copper lines and pads polish more quickly
in the soft copper center than on the harder barrier/ILD edge.
Dishing can thin the wire or pad, causing higher resistance wires or
low-reliability bond pads. Erosion occurs when narrow arrays of
copper and ILD polish more quickly than non-patterned areas,
thinning wires and increasing their resistance. Erosion can also
result in a sub-planar dip on the wafer surface. When the subsequent
layer of interconnect is completed, a shallow ˇ§poolˇ¨ of copper can
fill this dip, causing short-circuits between adjacent wires. Copper
or barrier residue caused by CMP underpolishing can also short
circuit the interconnect lines and cause device failure. To prevent
this possibility, most wafers are slightly overpolished. However,
severe overpolishing can thin the copper lines, both increasing
circuit resistance and the possibility of pooling on the next layer.
Therefore, to maintain high production yields, the CMP process must
be locally monitored on various test structures. These will indicate
whether the polishing process remains within the desired parameters
on structures of differing patterns and densities, and whether the
copper, barrier, and ILD are locally polishing exactly as required.
While a generalized large-spot in-situ CMP endpoint detector will
help control the CMP process in production, small spot, localized
monitoring will also be required in order to maintain high yield and
to catch mis-processing early.
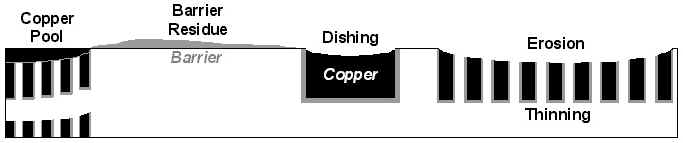
Figure 1. Common CMP mis-processing
problems result from the different polishing rates of copper,
barrier, and ILD. |